The principles underlying the TMI TATSUMI brand are impeccable quality and complete product safety for the consumer and the environment. Our production sites (there are already more than fifty all over the world) are certified according to all international standards (ISO / TS 16949: 2009), and the manufactured products correspond to the premium level, meeting the most stringent quality standards.
The standards for monitoring the conformity of manufactured auto components to the specified parameters are such that products under the TMI TATSUMI brand fully comply with the requirements of original parts supplied to the cars’ assembly lines. What's more, many of our spare auto parts are manufactured at the same factories that supply auto parts to the world's leading automakers.
The TMI TATSUMI brand produces an extensive range of premium automotive components and spare parts of various product groups. The following product groups are among them:
- Autocomponents of brake systems;
- Autocomponents of transmission systems;
- Suspension parts;
- Autocomponents of cooling systems;
- Autocomponents of filtration systems.
Products under the TMI TATSUMI brand meet the stringent requirements of the global automotive component market and meet the expectations of our customers. For example, all filters we produce are subject to pressure tests for tightness and comply with the standards of European and Asian countries for the degree of purification, capacity and flow resistance. And the components of the braking systems fit into the strict frameworks of the requirements of the legislation of the EU countries, in particular, they fully comply with the E-Mark standard.
The guarantee of the quality of premium products manufactured under our brand is high-quality raw materials. Our careful selection of suppliers of raw materials ensures high efficiency in the production of spare auto parts at all stages.
Each product manufactured under the TMI TATSUMI brand has a special quality certificate that guarantees the efficiency and durability of its work, as well as complete safety - both for the consumer and for the environment. All auto parts are covered by a two-year warranty from the date of purchase.
Our numerous staff of technologists, engineers, technical specialists is constantly working to improve product’s quality. To offer you the best spare parts and auto components, our specialists work closely with world leaders in the production of auto components, introducing technical and technological innovations actively into the production process. In addition, we are constantly analyzing the market in order to adjust timely the release of products for future demand’s changes. Besides, we are trying to reduce the cost of our auto components for the end user due to a well-built logistics system, production volumes, as well as reducing production costs.
The fundamental approach to the production of TMI TATSUMI spare auto parts is based on quality, innovations and modern needs of the global automotive parts market. Our product range meets the broadest needs of car owners around the world.
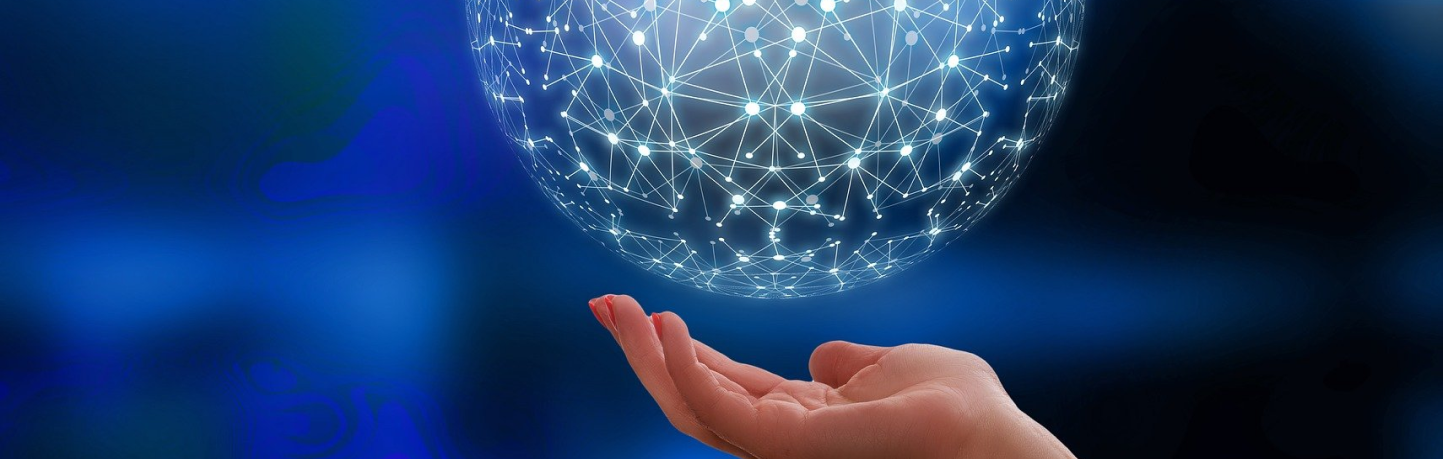
Scientific approach and innovation are at the heart of any successful modern high-tech enterprise. TMI TATSUMI engineers and specialists are constantly looking for new breakthrough solutions in the field of materials science, optimization of technological processes in relation to the production of automotive parts.
Every year, our specialists carry out several serious research projects to improve the quality of products and improve individual stages of the production cycle.
The emergence of new technologies does not always directly affect the manufacturing sector. It so happens that innovations are introduced in related areas of work - for example, in product testing, in technologies for assembling components, in the logistics of supplying parts, raw materials, equipment, etc. Even if the production process itself remains unchanged, the introduction of new solutions in related areas allows you to reduce the cost of a variety of resources - this can be transport costs, loss of time, energy losses, etc. expand the scope of delivery at the same price (for example, add fasteners or replaceable gaskets to a repair kit, etc.).
Scientific research by TMI TATSUMI specialists is carried out in close cooperation with many external scientists and employees of the automotive industry around the world. This approach achieves impressive results and has long been proven to be effective.
Well-organized scientific research is the basis for the successful production of high-quality products, therefore a serious industrial organization should pay close attention to them. In a competitive environment, the release of attractive products at affordable prices that meet all the requirements of buyers is the key to success. Based on this, the presence of well-equipped laboratories for conducting scientific research in a variety of areas is necessary in order to look confidently into the future.
As you know, the range of TMI TATSUMI spare parts and auto components is constantly changing (and most often towards expansion). To set up the release of any new part, it is necessary not only to prepare the production line and press the start button, in fact, everything is much more complicated. First, you need to build a detailed theoretical concept of future production, taking into account all factors, costs, interaction with other production areas, etc. It is necessary to go through the stages of modeling all processes in various modes, analyze all the scenarios obtained, and only after building the entire process “on paper”, you can proceed to debugging the line and launching production.
Specialists of TMI TATSUMI, thanks to the conducted research, from year to year introduce new innovations into production, thus making their contribution to the treasury of scientific and technological progress.
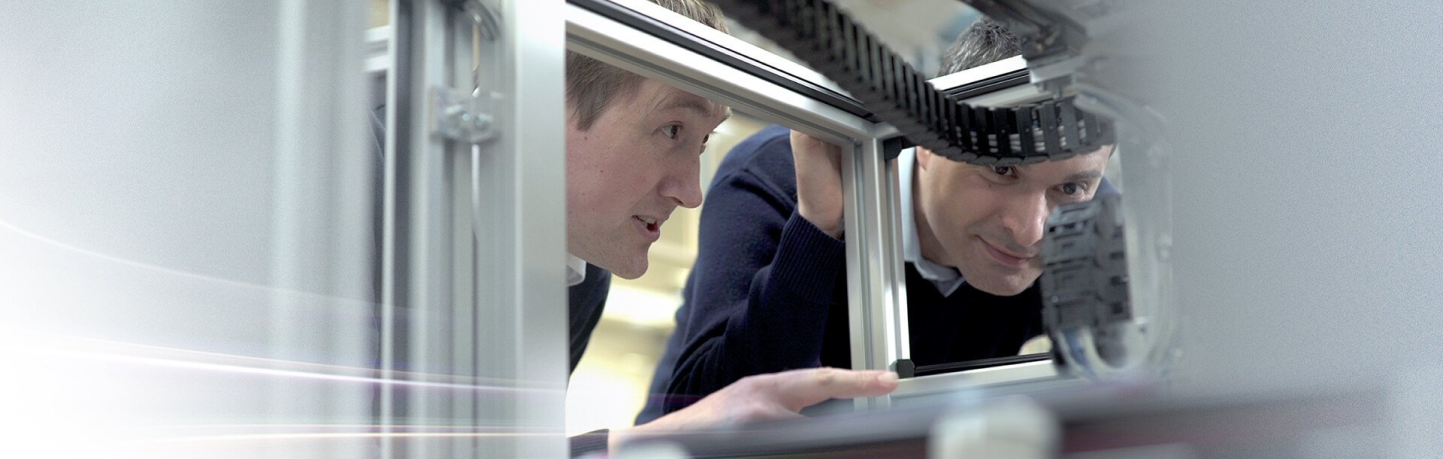
Reliable quality control and permanent testing are one of the most important parts of any modern production process, especially auto spare parts, which directly affect the road safety. Each our automotive component undergoes the highest testing in order to meet the strictest and rigorous legal requirements. What is more, TMI TATSUMI’s engineers pay much attention to the choice of materials that will be used in the production process.
The raw materials used and the final products of TMI TATSUMI brand are regularly tested for a variety of parameters in specialized production laboratories, which all our production sites are equipped with. Such control makes it possible to ensure the quality of produced spare parts at the level of requirements for original parts (and even higher) supplied to automobile assembly lines.
Careful selection of suppliers of raw materials used for the production of auto components enables us to minimize rejection in the production process and also makes it easier to ensure that products comply with the most stringent legal regulations.
In order to offer our customers the best premium spare auto parts at affordable prices, we have introduced strict control over the use of various chemical and metallurgical raw materials during the production process - we have worked out various detailed material specifications. Their aim is to control the use of unacceptable chemical components that may have an impact both on the environment and people’s health. Factories that provide TMI TATSUMI brand with auto parts have their own chemical analysis laboratories.
Strength testing of used steels and alloys is one of the most important areas of control laboratories’ work as one of the key characteristics is strength, especially in such product groups as bushing, silent blocks, suspension parts and control arms. The laboratories that are situated at factories investigate the quality of materials before using them in the production process. The results obtained from conducting strength tests on materials give a good indication of the quality of the material and its suitability for its intended end use.
What is more, some material can be tested for impact resistance using various methods including Izod and Charpy methods. It is common knowledge such tests are useful for comparing the relative impact resistance of different materials. This is especially important in the production of spare auto parts, which must be safe and durable.
A lot of automotive components, particularly metal, are at risk of corrosion that can lead to costly repairs and cause considerable car damage. Besides, in some cases, corrosion can even cause an accident due to the loss of strength and destruction of parts. We conduct different tests, which can help our engineers to select material types and refine designs to minimize susceptibility to the effects of corrosion. As a rule, these corrosion tests typically involve the spraying of a salt solution in a testing chamber at 35°C. These researches help to select the most resistant materials and to develop effective protection measures for corroded surfaces.
Some of the auto components, for example, the elements of car’s cooling system or filtration system, are exposed to adverse weather conditions. Our testing complex is aimed at simulating different weather conditionals so that it is seen whether the produced auto components are sustainable or not.
We carry out not only testing in accordance with recognized specifications and test methods, but also try to develop our own control and quality programs, first of all, for detailed control of the parameters of manufactured spare parts in order to optimize all technological processes, reduce costs and ensure an impeccable final result.
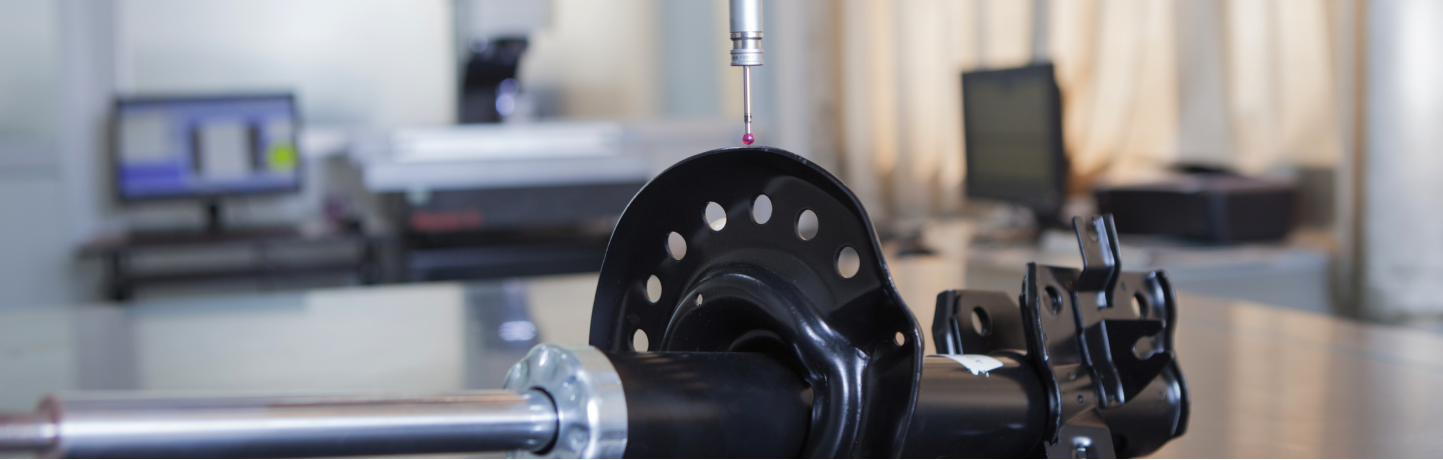
Striving to maintain the products’ highest premium quality and safety are the fundamental principles of the TMI TATSUMI brand. That’s why we consider that only modern, well-equipped manufacturers with the most modern technologies can take part in the production process of auto parts, which fully meet all the requirements.
All production sites that supply auto products for the TMI TATSUMI brand are certified and meet all the international quality standards. In addition, TMI TATSUMI’s spare parts correspond to OE quality and often even exceed it.
Our products fully comply with the strictest requirements of the world automotive spare part market. Due to their product group, auto parts can have one or several different certifications, confirming the high level of their quality and safety. For example, the components of brake systems TMI TATSUMI match with the requirements of the EU legislation, and all our produced filters are tested for impermeability under pressure: they meet modern European and Asian air purification requirements.
TMI TATSUMI products’ certificates are a confirmation of the excellent performance and functional properties of the manufactured spare parts. These documents confirm the resource potential of each individual auto part. It can be said that a certificate is a confirmation of the use of effective development technologies in the modern world of automotive products. In the meantime, there is no need for customers to worry about it. We try to do our best for our clients and we care about the quality of production certification.
All the factories that supply auto products for the TMI TATSUMI brand are ISO/TS 16949:2009 certified. It is also worth noting the fact that the quality of spare parts and automotive components produced at these production sites is confirmed by a two-year warranty, which starts from the moment they are sold to the client.
The TMI TATSUMI products have certificates that confirm their best quality. Spare parts possess ISO certificates as well as special certificates that are needed only in few world regions, for example, DIN EN ISO 9001, QS 9000, VDA 6.1, and UNI EN ISO 9001:2000. Moreover, we also correspond to JP standards, which are one of the strictest in the world, as well as to national (BS, ASTM, JASO) and international (ISO, EN, SAE) standards.
Continuous improvement of production processes, inculcation of new technologies, multi-stage quality control of manufactured products, and improvement of logistics allow us to look confidently into the future and gratify customers with the opportunity to purchase premium quality automotive components at affordable prices
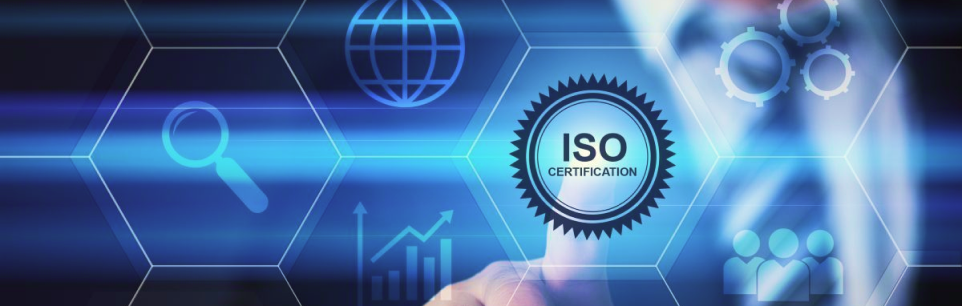